In high-risk industries like oil and gas, downtime compounds into lost revenue, missed quotas, safety exposure, and compliance risk. Whether the trigger is a shorted relay, a miswired PLC, or thermal overload, the root often traces back to a control panel. What many operators dismiss as “just a box” is in fact the nerve center of automated control. If that system is poorly designed or misbuilt, the cost is measured in hours offline, expensive equipment resets, and pressure from leadership. At G&C Optimization, we help companies remove that risk through intelligent, standards-based design. It starts with building industrial control panels that function reliably.
Is Your Control Panel a Point of Failure or a Strategic Asset?
Is Your Control Panel a Point of Failure or a Strategic Asset?
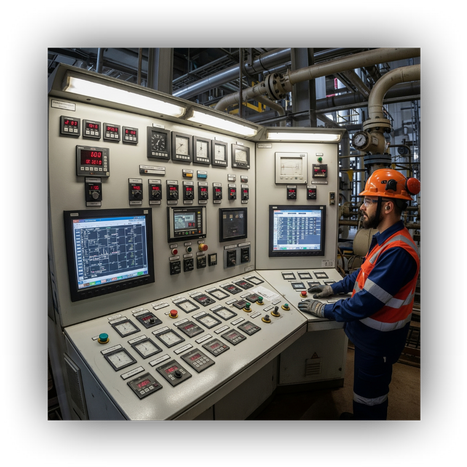
Beyond the Box
Industrial control panels aren’t commodities. They’re engineered systems that control critical plant processes like well pad automation and pipeline telemetry. Whether you're deploying an oil control panel in the Permian or operating SCADA infrastructure on the Gulf Coast, the build quality behind your panel determines operational stability.
A UL 508A certification is a documented build standard for control panels that limits liability and meets insurance and regulatory demands. G&C’s control panel shop builds to UL 508A requirements, covering component layout, wire sizing, overcurrent protection, and thermal management.
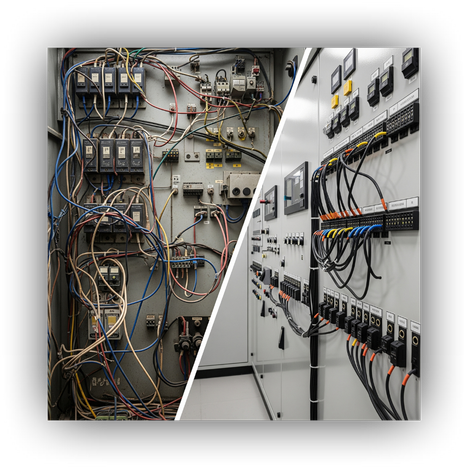
Panel Quality Shows Up on Your Balance Sheet
Every decision about panel design—from the enclosure rating to the HMI logic—either adds friction or removes it from your production system.
-
Uptime & Reliability: High-quality terminals, neatly routed conductors, and grounded enclosures reduce the chance of faults and simplify future diagnostics. That means fewer trips to the field and faster troubleshooting.
-
Process Efficiency: Logical PLC programming, intuitive labeling, and expandable IO layouts enable better automation and reduce the risk of human error. Over time, these efficiencies cut manual labor and speed up response cycles.
In the field, the difference between a well-built industrial control panel and a budget one often becomes clear during the first unplanned event.
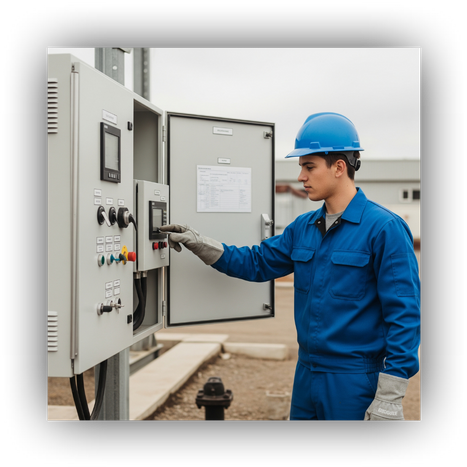
The Cost of Cutting Corners
When you save money upfront by going with the lowest bid or a non-certified shop, here’s what often happens:
-
Your technician can’t trace a fault because the wiring diagram doesn’t match the build.
-
Components burn out early due to thermal load miscalculations.
-
A regulator flags the panel because it lacks UL 508A labeling, requiring retrofitting or replacement.
Retrofitting a failed panel after installation often costs 2–3x more than getting it right the first time. The unplanned downtime adds even more to the bill!
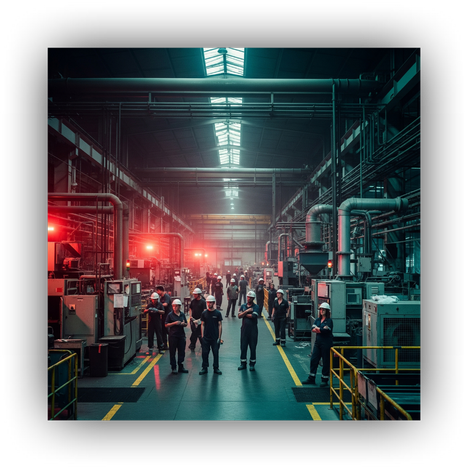
Every Minute Counts
Time lost on a production line disrupts upstream and downstream planning. That’s why our panels are designed for speed of service. Panels are cleanly labeled, documentation matches what’s built, and future add-ons are anticipated. We’ve seen operators waste hours tracing unlabeled wires or trying to replace an undersized breaker because the shop didn’t account for future load growth.
Get Ahead of the Next Problem
Choosing certified construction protects against code violations, electrical hazards, and rejected panels during inspections. More importantly, it gives your team confidence that what gets installed will run reliably and safely, shift after shift. To discuss how our industrial control panels can support your business objectives, schedule a consultation with G&C Optimization today.